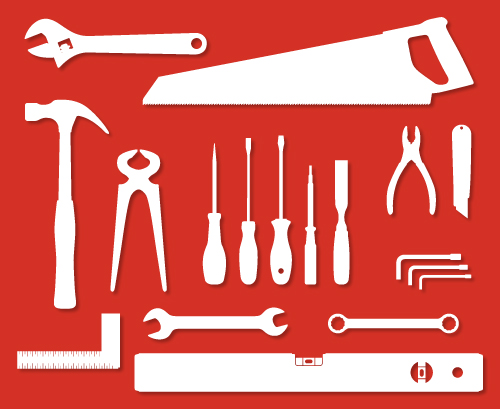
Any kaizen event will reveal how one small incremental process improvement can be worth significant bottom-line impacts. Kaizen, Japanese for “improvement” or “change for the best,” refers to philosophy or practices that focus upon continuous improvement of processes in manufacturing, engineering, and business management. When used in the business sense and applied to the workplace, kaizen refers to activities that continually improve all functions, and involves all employees from the CEO to the assembly line workers. It also applies to processes, such as purchasing and logistics, which cross organizational boundaries into the supply chain. By improving standardized activities and processes, kaizen aims to eliminate waste (lean manufacturing). Kaizen was first implemented in several Japanese businesses after the Second World War, influenced in part by American business and quality management teachers who visited the country. It has since spread throughout the world and is now being implemented in environments driving productivity.
Kaizen: Simply Tools with Lean Impacts
Lightbox is just a tool to quickly generate design information that can create CNC produced part protection. This part protection considers part characteristics (Class A surface, odd appendages, weak/strong points) and correct packaging materials to allow the part to flow and move through the facility with the least amount of risk.
Shadow Boards, Kit Trays, Dunnage, Rails and Partition Trays are other elements to improve a material handling and manufacturing operation process.
Troligiq USA’s Luman Temby reported, “When parts are moved in the plant, damage can result from forklifts and transportation, people, other parts, or process. Custom packaging and part protection solutions provide answers to reduce risk in part movement and handling in all of those areas.”
Creating customized visual I.D. tool boards, error-proofing shadow board and part protection trays on the LightBox all are quality driven considerations that eliminating part damage and process errors.
Best practices are demonstrated in two specific areas of quality, part damage and process errors. Part damage results from parts not being sufficiently contained, protected, or packaged thus being subject to conditions that can impair quality (dents, scratches, and impacts). Process errors result from the wrong type or quantity of parts arriving to an operator that can cause process delays and losses.
Temby strongly suggested, “Designing integrated material flow, material presentation, and material protection systems using a variety of methods and materials is critical. The purpose of these systems is to consider how a part moves through a facility or value stream and reduce the risk of damage at each step.”
The Role of Expert System Integrators for Best Practice
Integrated solutions often falls to the systems integrator with whom the customer has built a trusted relationship. The full gamut of services based in wisdom and experience of potential solutions options is critical. Sadly, the majority of system integrators in material handling can be described as order-takers. Rather than actively seeking all the possible integrated automation solutions for the end-user customer, products are ordered, delivered, and installed. Trilogiq USA, based in Livonia, Michigan, pioneered the holistic team consultative approach using an evaluation methodology. Lean manufacturing is an elevated concept, yet much of the waste to be eliminated and continued process improvement can be made in the very smallest incremental improvements. Strategically planning to work with a singular expert system integrator to analyze, assess, and acquire the best overall integrated solutions may reveal something as simple as tubing selection to achieve lean best practice results.
Tubing Selection Driving Productivity
Bob Rechul, a sales engineer with Trilogiq USA, brings nearly two decades in the tube and joint field where he processed reviews to reduce waste, improved manufacturing quality, reduce cost, and improved operator ergonomics. “Tubing is one area that manufacturers can immediately realize increased productivity while lowering manufacturing costs. Simply using the best tubing solution often results in a 12-15 percent increase per year in productivity,” shared Rechul.
Tubing expertise is one of the shortest paths toward lean results. Holistic material handling experts often define the elimination of poor choices and rapid identification of best options. Rechul worked to implement 5S and ran kaizen events at General Motors, Ford, and Chrysler as well as many aerospace, medical device and, food service industries.
Any vendor can sell tubes and joints; tubing improvements must be combined with all of the elements of efficient material handling elements for holistic process improvement; the product approach is not a lean best-practice. A partnership approach with the customer from conception to long after the execution is required to ensure products and solutions surpass the needs of manufacturing customers.
Quality Assurance is best achieved when tube fittings are designed, manufactured, quality controlled and distributed to be totally “interchangeable.” The precision manufacturing of products to stringent tolerances under rigid quality control procedures ensures the safety, performance and reliability of service. The extrusion process is the critical part of ensuring the integrity of a complete solution. The quality of this plastic coating (extrusion) is dependent on the raw plastic chosen for its durometer. The plastic must be suitable to the fittings used for the complete assembled solution. If improper plastic material is to extrude the tubes, the fittings will not properly or safely adhere to the extrusion. The thermoplastic extrusion process to coat their steel tube must provide several strength improvements over powder coating and other coating alternatives. Damaged tubes cost big money, requiring diagnosis, replacement, and repair. This down-time is a huge waste that can be easily avoided. Tubing connectors with a non-slip nub, which grips the thermoplastic coating, is considerably better without marking or damaging the tube. Inspection is always an import job by tube and connector suppliers. Tube fittings are often manufactured in accordance to conform to the ISO 9001:2000 Quality Standard.
From tubing, to CNC, to Lightboxes, a holistic approach can be observed, quantified, and measured in quality. In material handling, the three functional areas are material flow, material presentation, and material protection. Tube and joint solutions typically function in the first two areas where CNC and Lightbox solutions work in the third. The impact on quality, specifically part quality, is different in each area.
Material flow is measured when parts are moved in the plant; damage can result from forklifts and transportation, people, other parts, or process. Tube and joint solutions (along with Automated Guided Carts (AGCs), autonomous driverless mobile robots, and integrated part protection) help to address each of those causes of errors by right sizing the material flow and better containing the parts when moved.
Material presentation is critical because when parts are not presented to the operator at the line in a safe, ergonomic fashion, damage can often result when the parts are moved awkwardly. Tube and joint structures provide the best ergonomic presentation of parts. They not only to improve environmental, health, and safety (EH&S) measures, but also to allow the operator to handle parts in the easiest way to respect the part’s quality integrity.
Material protection is the most valuable area of part quality that holistic integrated lean solutions providers can implement. This discipline can exist independently, or work in conjunction with material flow and material presentation. Experienced and thoughtful systems integrators consider how parts are best packaged, moved, and presented until they are finally used. Most of the damage to parts inside of a manufacturing facility occurs due to poor protection and packaging design at some point in the process.
Kaizen is a daily process, the purpose of which goes beyond simple productivity improvement. It is also a process that, when done correctly, humanizes the workplace, eliminates overly hard work (“muri”), and teaches people how to perform experiments on their work using the scientific method and how to learn to spot and eliminate waste in business processes. The process suggests a humanized approach to workers and to increasing productivity.